Case Western Reserve leading research to develop zero-carbon, electrochemical process to produce iron metal as part of U.S. Department of Energy effort
Case Western Reserve University chemical engineer Rohan Akolkar is leading a research team working to develop a new zero-carbon, electrochemical process to produce iron metal from ore.
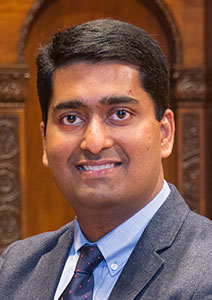
If successful, the project could be a first step toward eliminating harmful greenhouse gas emissions by eventually replacing century-old, blast-furnace ironmaking with a new electrolytic-iron production process.
Reducing iron ore to metal is carbon- and energy-intensive, leading to significant carbon-dioxide emissions that drive global warming.
“We don’t use carbon at all in our process, so iron could be produced cleanly,” said Akolkar, the Milton and Tamar Maltz Professor of Energy Innovation at the Case School of Engineering. “Between 7-8% of greenhouse gas emissions are due to steelmaking, and the industry has been practicing the same technology for more than a century. This may not be sustainable.”
Ironmaking in a blast furnace involves combining carbon and iron ore at very high temperatures to “reduce” the iron ore to “pig iron,” the key raw material in the steel industry, according to the U.S. Department of Energy (DOE). But when carbon reacts with oxygen from the ore, the result is carbon dioxide gas.
Recently, Akolkar’s team won a $1 million grant from DOE’s Industrial Efficiency and Decarbonization Office.
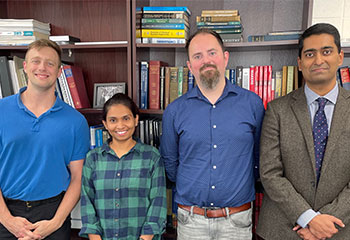
Case Western Reserve will lead a team that includes Lawrence Livermore National Laboratory (LLNL), the University of Arizona and Cleveland-Cliffs Inc.—the largest flat-rolled steel company in North America and a leading supplier of automotive-grade steel.
Just over a year ago, President Eric W. Kaler and LLNL Director Kim Budil signed an agreement to accelerate their institutional collaborations.
“Both of our teams have embraced opportunities to partner with enormous enthusiasm and ingenuity,” President Kaler said at the time.
Zero-carbon technology
Akolkar said his team has developed a unique chemistry and process—a novel molten salt electrolysis method—that keeps sustainability front and center.
“It is vital that our process is cost-effective for it to have a transformative impact to industry and society,” Akolkar said. “Our process has the benefits of being low-cost and can achieve high rates, but also while using environmentally benign chemicals. Together, these advantages will help us develop not just a novel process, but also one that is truly techno-economically viable.”
Akolkar’s team, which includes Case Western Reserve research engineer Nicholas Sinclair, has pioneered molten-salt electrolysis methods for various metals.
Using molten salts, electrochemistry can be performed at moderately high temperatures. This allows electrolytic metal production to be practiced cheaply and at industrial scale.
Akolkar also recently demonstrated use of this technology for sustainable domestic production of critical metals such as neodymium.
Broader decarbonizing effort
The DOE announced the award as part of a broader $135 million initiative involving 40 projects at universities, national laboratories and companies in 21 states. The agency’s goal is to reduce industrial carbon pollution and move the nation toward a net-zero emissions economy by 2050.
Case Western Reserve’s project is among 10 focused on Decarbonizing Iron and Steel. The DOE also funded projects for decarbonizing chemicals, cement and concrete, food and beverage products, and paper and forest products, as well as projects to decarbonize across multiple industries.
For more information, contact Mike Scott at mike.scott@case.edu.