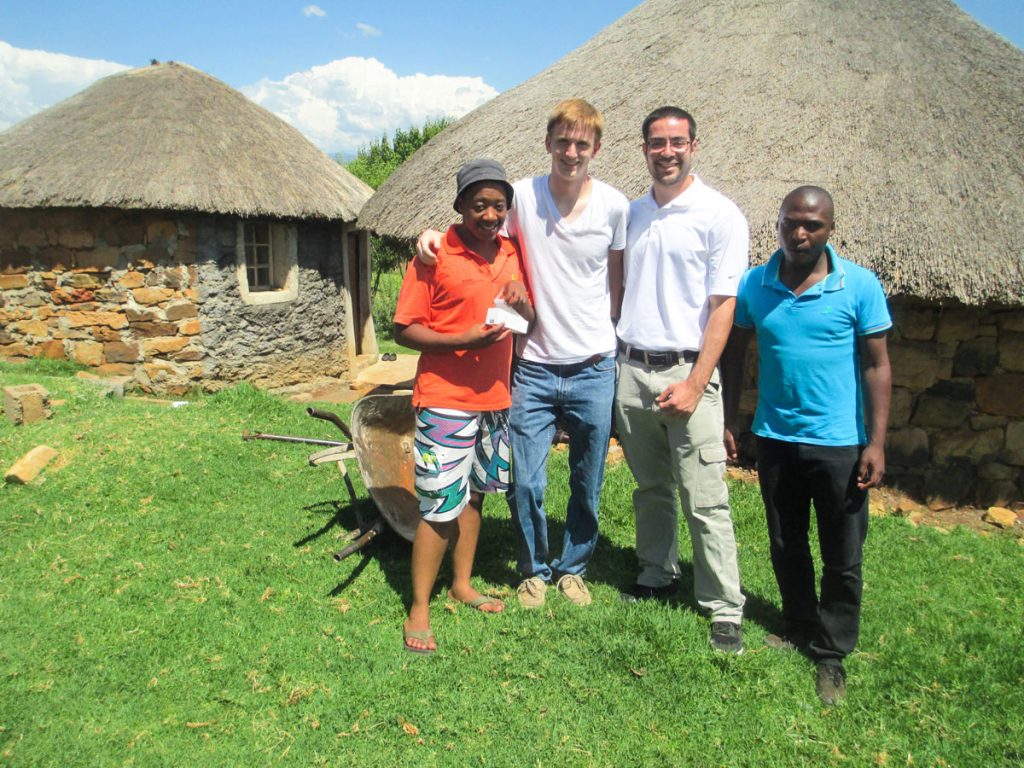
Earlier this month, a pair of Case Western Reserve University engineering students field tested their foot-powered cell phone charger in rural villages of the Kingdom of Lesotho, a small country surrounded entirely by South Africa.
“A lot of people have cell phones but no way to charge them,” said Samuel Crisanti, 19, a sophomore from Windsor, Conn. “In the country, 40 to 50 percent or even 60 percent have cell phones but only a quarter have access to electricity. It takes some a day-long ride by cart to a city where they have to pay to charge their phone.”
Crisanti and classmate Ian Ferre, 20, of Louisville, Ky., teamed up last year to build a solution in a class called “Engineering for the World’s Poorest,” taught by Daniel Lacks, a chemical engineering professor.
Lacks liked their idea and initial work so well he offered to let them skip writing a final paper if they would instead write an application for an U.S. Environmental Protection Agency grant. Crisanti and Ferre won a $15,000 grant that they used to buy supplies and build versions of the charger this year, and pay for the trip.
They kept the equipment under Ferre’s bed in the residence hall room they share, and they built at the university’s think[ box ], a center that offers space, equipment and training to convert designs into tangible products.
Lacks invited them to come to Lesotho with his senior design class, whose members designed and built solar electric systems for families. While they did that, Crisanti and Ferre met with farmers and others who earn $1 to $2 a day, to gauge their interest in the charger.
“We wanted to see what kind of phones the people use and what’s most useful to them,” Ferre said.
The sophomores have built several prototypes that rely on ratchet mechanics. Gears change the motion of a foot pressing on the pedal (think of a pedal for a drum set’s base drum, not a bicycle pedal) into circular motion that powers a generator. Like a ratchet tool, the gears spin only in one direction.
Pedaling can generate enough energy to recharge a phone and power a small lamp with a light emitting diode bulb. It can be done sitting or standing. The students spent about $12 to 3D print the latest lightweight and portable version.
Ferre and Crisanti will compete for a $75,000 EPA grant in April. If they win, they plan to buy injection molds for the plastic parts. The plastic injected would be sturdier and more durable than that used in printing and, by mass-producing, they expect to cut the cost to no more than $5 each—a price villagers can afford.