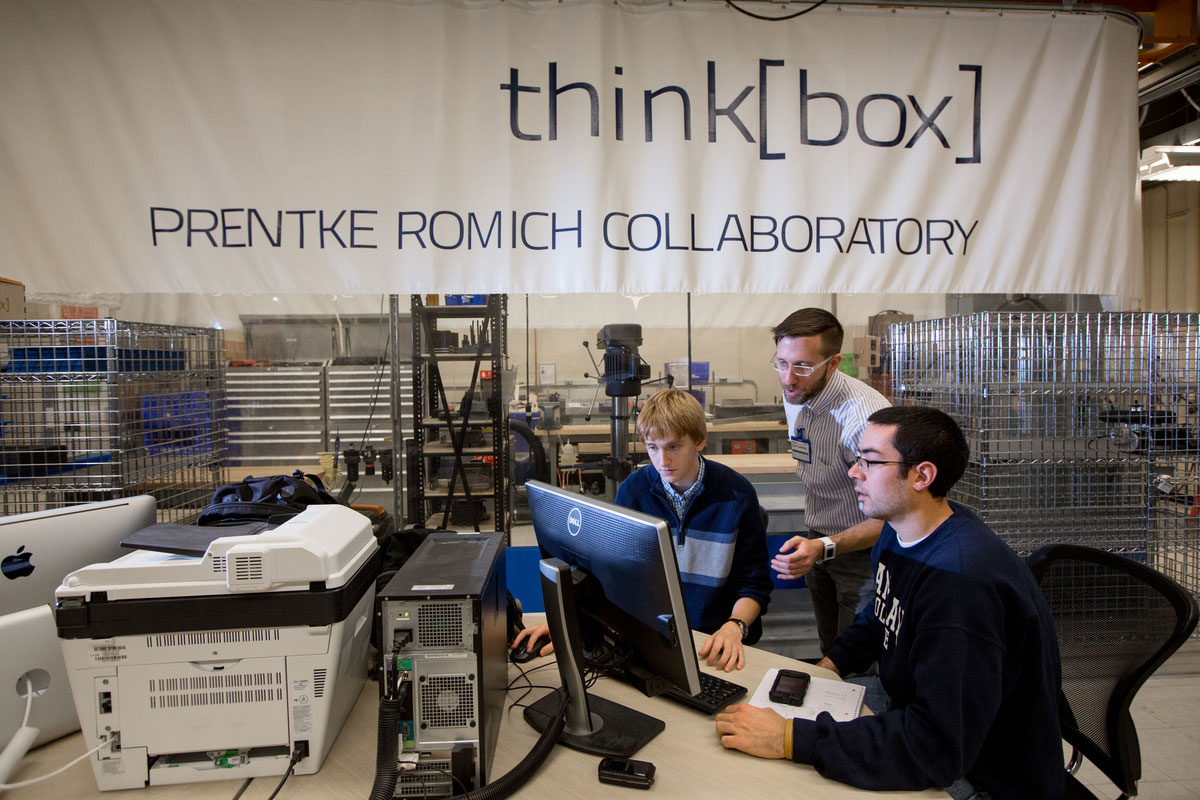
The $700,000 project is among 15 recently announced by America Makes, the National Additive Manufacturing Innovation Institute in Youngstown, which is spearheading next-generation manufacturing technologies based on 3-D printing. The projects are winners of America Makes’ second round of funding.
Researchers and business partners developing the new 3-D process aim for a quick conversion.
“The goal is to have an impact on commercial manufacturing as soon as possible,” said James McGuffin-Cawley, chair of the Case School of Engineering’s Department of Materials Science and Engineering and one of the project leaders.
Badri Narayanan, manager of materials research at Lincoln Electric, expects the project to push the boundaries of this process to generate structural components and functional surfaces.
Rounding out the research team is Roger Quinn, professor of mechanical and aerospace engineering at Case Western Reserve, and Paul Denney, senior laser applications engineer at Lincoln Electric Automation.
In addition to Cleveland-based Lincoln Electric, the industrial partners include: RTI International Metals (Pittsburgh), a leading producer of titanium mill products and components; rp+m (Avon Lake, Ohio), a diversified engineering company that uses 3-D printing technologies to create client-specific solutions; and AZZ/WSI Inc. (Norcross, Ga.), a leader in developing and delivering design repairs, component upgrades and specialty maintenance services for energy intensive industries.
Lincoln Electric is an international leader in the design, development and manufacture of arc welding products, robotic arc welding systems, plasma and oxyfuel-cutting equipment, and in the brazing and soldering alloys market.
Lincoln Electric pioneered the laser hot-wire process for steel cladding, and has shown it to be adaptable to additive manufacturing through a pilot project funded by America Makes in the first round of funding.
In this new process, metal parts are built up using a combination of wire-feed, laser melting, and resistance heating to achieve a high degree of metallurgical control in concert with a high deposition rate. This project, supported by federal and private money, will explore the adaptability of this process for building parts with titanium- and nickel-based alloys for aerospace and marine applications.