A team of researchers at Case Western Reserve University is part of a national effort to “reimagine” steel production, developing an innovative and low-cost process that could replace blast furnaces for ironmaking.
If successful, officials at the U.S. Department of Energy (DOE) believe the effort could reduce greenhouse gas emissions in steelmaking by as much 85%. The DOE recently announced a $19 million investment over four years for the federally supported Argonne National Laboratory to lead the multi-institutional Center for Steel Electrification by Electrosynthesis (C-STEEL).
C-STEEL is part of the DOE’s Industrial Heat Energy Earthshot initiative, seeking to significantly cut emissions from energy intensive processes. Case Western Reserve will receive $1.1 million of that investment. Other funded members of C-STEEL include: Oak Ridge National Laboratory, Northern Illinois University, Purdue University Northwest and the University of Illinois Chicago.
“Steel has a major impact on everyone’s lives and our economy,” said Rohan Akolkar, the Milton and Tamar Maltz Professor of Energy Innovation at CWRU. “Steel is crucial to transportation, infrastructure, buildings and more. But, in the industrial sector, steel production accounts for a large percentage of greenhouse gas emissions.”
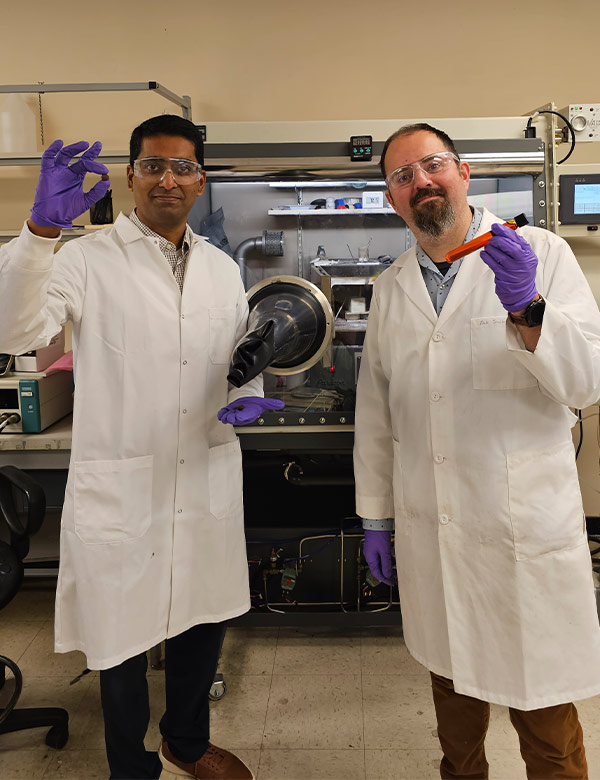
Akolkar’s laboratory has pioneered a new electrochemical process that could potentially decarbonize steelmaking. But much of the fundamental science behind this process is still in its infancy. C-STEEL will allow Akolkar to collaborate with researchers at Argonne National Laboratory to discover electrolytes that could help make steel greener using electrochemistry.
Akolkar said the most energy intensive step in steel production involves converting iron ore into purified iron metal using blast furnaces. This requires temperatures approaching 2,700 degrees Fahrenheit—hotter than an erupting volcano.
Nicholas Sinclair, a research engineer at the Case School of Engineering and a member of Akolkar’s Electrochemical Materials Fabrication Laboratory, said researchers are actively exploring new methods. Among them: an “electrodeposition process” that involves dissolving iron ore in an electrolyte medium and using electricity to initiate a reaction that deposits useable iron metal at an electrode.
Another goal is “exerting precise control over the structure of the metal deposits so that they can be incorporated into existing downstream processes of steelmaking,” Sinclair said.
C-STEEL’s target is to develop a process that essentially eliminates heat demand, achieving even higher reductions in greenhouse gas emissions by 2035.
“C-STEEL has ambitious targets, but a huge reward if successful,” said Brian Ingram, the C-STEEL director and an Argonne group leader and materials scientist. “We are delighted to work with CWRU researchers Akolkar and Sinclair. Their pioneering approaches to energy efficient metal electrodeposition are essential to the success of C-STEEL.”
For more information, contact Colin McEwen at colin.mcewen@case.edu.